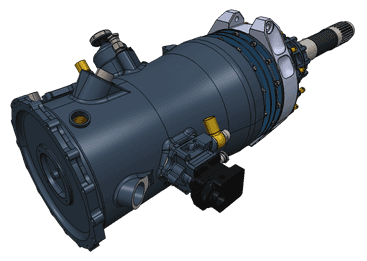
Beginners guide to CAD data
Prepare your business for Industry 4.0, learning how 3D data is presented in CAD.
Get the guide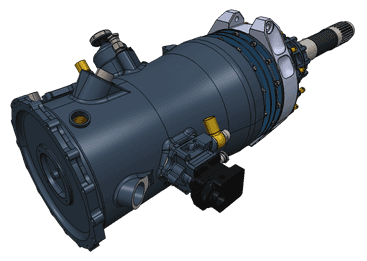
Beginners guide to CAD data
Prepare your business for Industry 4.0, learning how 3D data is presented in CAD.
Get the guideWhen talking to prospects and customers for a few last years we have been observing very distinct levels of skills and knowledge in CAD, 3D modeling, computational geometry and other domains relevant when working with 3D data. Some users are very familiar with taking second partial derivatives d2S/dudv whereas others have hard time to understand the concept of a water-tight mesh.
So after some thinking about how we could help those users to get up to speed faster and do their jobs better, I came up with this idea of writing a brief crash course on CAD data. Of course, it does not pretend to be exhaustive (it’s a crash course in the end of the day) or even well balanced. Its objective is rather just to scratch the surface, to give some minimum background and encourage a professional to do his/her own research afterwards. I warmly welcome comments, suggestions and even corrections if you notice something to be incomplete.
The topics I’m going to cover include:
- How did this all begin?
- How is 3D data presented in CAD?
- Precise geometry and tessellation. B-Rep’s and meshes.
- Parts and assemblies.
- Meta-data (names, id’s, user-defined properties, etc).
- Visual attributes (colors, materials, transparencies, textures).
This blog post series will be written and published in the course of coming weeks, so chances are some topics can be added or adjusted as they get created. As for any business executive, time is always in short supply for me, so no promises of the timeline. But hopefully I will find bandwidth to complete the series without keeping you waiting for too long.
So, let's start.
Part 1. How did this all begin?
Up to 1960's the design process of a new ship, a car, or an aircraft would look as follows:
- Take a previous version or make a concept from scratch.
- Make a physical prototype. Run physical experiments (crash tests, aerodynamics tube, water etc). Adjust the design. Repeat.
- Make precise drawings. Manufacture.
- Release. Gather user feedback, introduce modifications to the design. Release a new version.
- Repeat.
Consumer products (from pencil to shoe, or electrical shaver and so on) would probably go through a similar yet simpler product lifecycle management (PLM).
With ramp up of the computer industry, large manufactures in 1970's started adopting numerical methods in various stages of the process: design, numerical simulation, manufacturing, data management.
This gave birth to the CAD/CAM/CAE/PDM industry – Computer-aided Design, Manufacturing, Analysis and Product Data Management. Later on an umbrella term – PLM (Product Lifecycle Management) – was invented to encompass all these areas.
There are numerous large/medium/small generic CAD/CAM/CAE systems and specific ones focused on particular problem domains. The latter can cover PCB (Printed Circuit Board) design, water/gas turbines, consumer products (such as shoes or even cardboard boxes), you name it.
When the industry was ramping up it was moving from traditional 2D data, such as drawing which is simpler, to 3D, which is able to transmit design ideas between humans much easier. This brought an obvious question - how can we mathematically describe that 3D data? This leads us to part 2 of our series.
Related readings:
Everything you need to know about CAD file formats
Next parts:
Part 2. How is 3D data presented in CAD?
Part 3. Precise geometry and tessellation. B-Rep’s and meshes.
Part 4. CAD model structure. Parts and assemblies