Digital twins are increasingly used to transform immense volumes of data into relevant insights in aerospace, automotive, manufacturing, healthcare, and many other industries.
Slingshot Aerospace, for instance, is developing the first digital space twin for the US Space Force to simulate possible incidents, calculate their impact, and assess responses. In the meantime, Orlando Economic Partnership (OEP), jointly with Unity, is going to build a 3D model of Orlando, Florida. The region's authorities plan to use this technology to predict the impact of new infrastructure projects and to attract potential investors. Finally, MWU Software developed Fetal Heart VR - a simulation tool for ultrasound training focused on Congenital Heart Diseases diagnostics.
Thus 3D experts have a large field to work at: creating precise replicas of a real-time object, bringing together data from multiple sources, running simulation and prediction analysis. This is the way Light & Shadows, a company founded in 2009, uses its 3D expertise to provide AR/VR hardware and software solutions for the improvement of design processes, industrial performance, marketing, and training.
Read below how CAD Exchanger ensured seamless 3D data processing inside XR Twin - Light & Shadows VR application.
Light & Shadows — digital transformation of the industrial processes
Light & Shadows is a B2B company located in France contributing to the digital transformation of companies via virtual and augmented reality applications. The company has four main areas of the business: LS Software, LS Solutions, LS Studio, and LS Academy.
- LS Software provides on-the-shelf AR/VR software suites working with CAD models and point clouds. Their most common use cases include assessment of the workstation ergonomics, creating Unity-based applications directly from 3D data or CAD scan models, and industrial painting simulation.
- LS Solutions, in their turn, develop custom web and mobile applications using WebGL, VR, AR, MR. These solutions are used for immersive product marketing, interactive learning experiences, industrial processes simulation and optimization.
- LS Studio is focused on high-quality 3D rendering for showcasing customers' products. The company produces images and videos for advertising and trade fairs, interactive product configurators for apps and websites, and other types of AR/VR demo content.
- LS Academy conducts training on Light & Shadows and third-party 3D products.
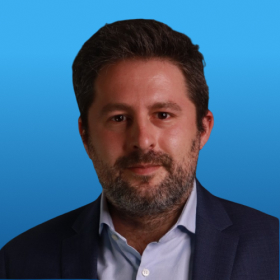
Jordane Richter
Light & Shadows stands out for its experience and mission. After 12 years of 3D data optimization for industrial purposes, customers autonomy remains the central point of the business. That is what led to the creation of the XR Twin — a plug-and-play application that allows its users to interact with their 3D CAD models in VR.
XR Twin — VR scenarios in the industrial context
XR Twin allows customers to visualize their production lines and interact with them using virtual reality. The tool is composed of an authoring module that lets the user import CAD files and elaborate scenarios and a simulation module that executes these scenarios in VR.
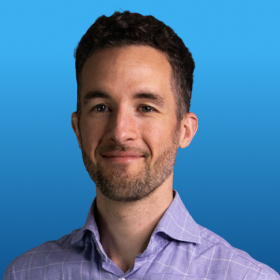
Antoine Lasnier
There are several typical use cases for using XR Twin: factory layout simulation, industrial workers training, production optimization, and ergonomics evaluation. The tool helps to figure out the best physical configurations of the production or assembly line, to improve cycle time and limit errors, and to optimize workstations, operator’s posture, and safety.
The challenge of 3D CAD files import
XR Twin tools simplified creating customized scenarios thanks to predefined environments, kinematic constraints, collision, joints, industrial library, and a panel of assets. XDE physics engine guarantees the precision of the simulation and the performance of the complex scenes animation. The only question left was the possibility of importing various CAD data.
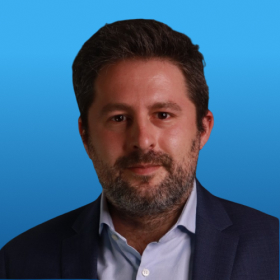
Jordane Richter
XR Twin is used by a wide range of different industries, so the solution needs to support the largest number of formats possible. Apart from the quantity of 3D formats, Light & Shadows had a solid list of requirements justified by the specifics of the Unity engine in particular and real-time interaction in general.
- Fast mesh generation. CAD data processing should go behind-the-scenes, invisible for users and without triggering sluggish system reactions.
- Easy and fast integration with Unity. As noted by Antoine Lasnier, Chief Operating Officer of Light & Shadows, many import solution imply complicated low-level implementation scenarios and full-fledged C# or C++ code.
- Seamless import of the CAD files. XR Twin users do not always have a background in 3D design, and they should not be aware of the underlying complexity of the 3D data and its optimization. From the customer’s angle the process should be as simple as drag and drop.
- Optimal quantity of polygons. For instance, the GPU of a VR headset may need to generate up to 90 frames per second for each eye. That’s why it is necessary to decrease the number of polygons without affecting the quality of the visualization to speed up the simulation.
- Optimal data precision. Interactivity, motion tracking, and simulation must respect the laws of physics, for example, during collisions or dropping of the object. It’s critical to find a trade-off between data precision and its volume to keep rendering realistic and performance high.
Bridging the CAD-to-Unity gap with CAD Exchanger
After six months of benchmarking available import solutions, Light & Shadows found CAD Exchanger SDK to be the best option. It provided decent results in both loading times and quality of the models, integration with Unity, and formats compatibility.
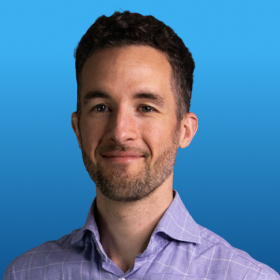
Antoine Lasnier
As mentioned by Antoine Lasnier and Jordane Richter, there are five key benefits that CAD Exchanger provides both for the business and its customers.
- Drag-and-drop simplicity. From the user perspective, the import of files looks fast and straightforward. Transfer of the data, its optimization, and healing are totally invisible, not distracting the users from their tasks.
- High speed and quality. Light & Shadows customers process their CAD files fast and build stunning immersive experiences with them.
- Fast integration. According to Antoine Lasnier, the first integration was faster than it was expected, thanks to the well-thought-out Unity plugin provided by CAD Exchanger: “In a few days, it was clear that the tool is really able to smoothly load 3D models in formats not supported by Unity itself.”
- Great customer support. What is the best strategy to treat specific CAD data? Why can’t this file be imported? What are the optimal triangulation parameters for this particular case? Whenever something was not clear, Light & Shadows always got a fast and accurate answer from the CAD Exchanger support team.
- Complete documentation. CAD Exchanger has a clear and structured API with comprehensive documentation of model data, usage scenarios, and converter processing. What’s more, there are example applications for most common use cases that could be launched and customized as needed.
Thanks to CAD Exchanger, Light & Shadows solutions are now compatible with most of the 3D file formats on the market, whether they are from CAD, BIM, or design software. And XR Twin users can maximize their benefits from digital twin technologies, creating a realistic simulation of industrial processes.
Read more case studies on CAD data integration into AR/VR or get advice on your application.
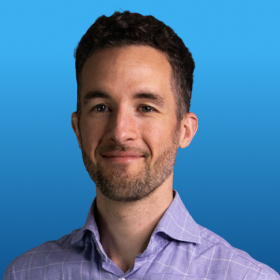