Prerequisites for surviving in today’s industrial market have been summarized in the principles of the Fourth Industrial Revolution. Industry 4.0 is based on informational connectivity, transparency, and digitalization. It requires correct and comprehensive data incorporated into the product’s digital models usable across all stages of the product lifecycle and all systems involved. Shipyard 4.0, respectively, requires an exhaustive coverage of all ship elements and their attributes applied for each and every downstream process: from design and manufacturing to pricing and end-of-life.
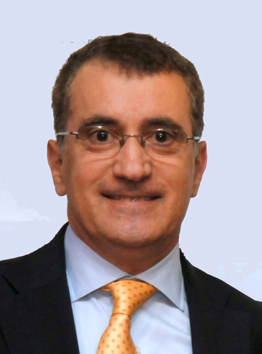
Jesús Ángel Muñoz Herrero
SENER Marine, with its half of a century experience in industrial innovation, started an extensive transformation process towards this new era long ago. The company developed its own multifunctional shipbuilding software - FORAN - and is progressively turning it into an all-encompassing data source. And this year, FORAN software will be acquired by Siemens topping up its ship-lifecycle services. Since 2012, CAD Exchanger has been an integral part of this process, providing technologies related to 3D data exchange in FORAN. Read the story of a collaboration that started with one CAD format support and made it to optimizing every bit of CAD data processing algorithms.
About SENER Marine
65 years of shipbuilding
SENER, with its grandiose projects in aerospace, infrastructure, energy, and marine, is indeed a Spanish market leader in the engineering and manufacturing business. Being founded in 1956 as a technical marine office, SENER now has 2,500 professionals providing state-of-the-art engineering solutions to the whole world. The company is designing a high-speed rail in California, developing an offshore LNG terminal in Argentina, connecting the Sinai Peninsula and Egypt with specially designed tunnels, inventing technologies for the Jupiter Icy Moons Explorer (JUICE) program to be launched by the Netherlands. “Soluciones de ingeniería al servicio de los clientes y la sociedad,” - that’s what their mission sounds like, which is translated as “Hi-tech engineering solutions in the clients and society service.”
SENER still stays committed to its original vocation represented by its SENER Marine subsidiary, which delivers on engineering and consultancy contracts for numerous shipyards, design offices, and ship owners all over the world. SENER Marine supports projects of various types of vessels and offshore structures, starting from the conceptual design and up to construction supervision. The company engineered a 1,200-passenger ferry vessel for South Korea and a stern trawler for China, assisted in repairing and modernizing of the Argentinian Navy’s icebreaker and consulted on keel laying in Tanzania, performed a feasibility study for the conversion of a harbor tug to use liquefied natural gas (LNG) and engineered the supporting structures for offshore wind generators, to name a few.
Shipbuilding CAD system FORAN
In 1965 FORAN, an in-house CAD/CAM/CAE system, was launched to simplify engineering calculations. As the 20th century advanced, SENER engineers felt the need to digitalize all the stages of the vessel design and gradually expanded the functionalities of the FORAN.
Now FORAN is used by 150 shipyard and design offices across 40 countries to design carriers, submarines, ferries, fishing vessels, icebreakers, trawlers, and other kinds of ships. The system covers all the stages of the vessel’s lifecycle up to its delivery to the shipowner: from initial design to the hull, machinery and outfitting detailed layout, from electrical design to drafting, from integration to PLM systems to immersive virtual reality solutions.
Thanks to this broad range of applications, FORAN end-users can be either conceptual designers elaborating the main volumes and spaces of the ship, or engineers who join the game after the contract is signed, or the shipyard’s staff managing validation of the design and production of the vessel. All the necessary information is stored in a single database and equipped with shipbuilding-oriented features.
The challenge of compact database vs data exchange
Each project created in FORAN covers not only geometry but also many other attributes, including the ones required for simulation, fabrication, stock management, materials definition, etc. Nevertheless, the database stores only the necessary minimum of information. For instance, instead of keeping a complete B-Rep representation of a cylinder, FORAN stores just the definition of where the cylinder starts, its radius and length values, as well as its axis orientation.
At the same time, FORAN is required to be capable both of reading external data and transmitting models to the downstream applications. At the detailed design stage, it’s necessary to import pieces of machinery and equipment designed by various third parties, while manufacturing and assembly steps imply extraction of the data depending on the production methods and tools involved.
This contradiction became acute in 2012 when FORAN aimed at integrating with two leading PLM (Product Lifecycle Management) tools: Windchill and Teamcenter.
The steps to a consistent CAD data processing by CAD Exchanger
Expanding 3D formats support
The preferred exchange format for connecting with PLM systems was JT, the standard one across the Siemens ecosystem. SENER Marine considered two ways to solve the problem: either to develop the solution themselves or to contract another company. The first option would have entailed the recruitment of new employees with corresponding knowledge and experience. Outsourcing the task was not that easy too, as developing the exchange algorithm from scratch would have taken a lot of time. On the other hand, CAD Exchanger already had expertise in multiple CAD formats and geometrical kernels interoperability.
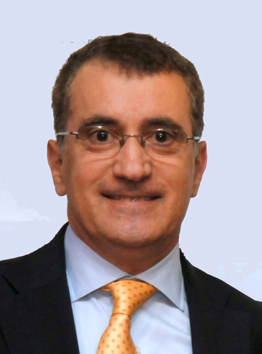
Jesús Ángel Muñoz Herrero
CAD Exchanger had a readily available functionality that our customers required. All that was left was matching the way CAD Exchanger and FORAN manage the data. Charged with a new task, CAD Exchanger not only enabled JT support but tailored its implementation to meet the customer’s specific needs, adding user-defined properties support, and further integrated STEP, IGES, DXF, and IFC formats support.
Implementing advanced mathematical algorithms
Collaboration between SENER and CAD Exchanger and further communication with customers determined that, apart from one single format support, the challenge went deeper: reading and writing other formats, improving conversion and other geometric algorithms performance, dealing with huge data volumes and tessellation.
In the following years, CAD Exchanger not only integrated numerous formats import and export but also has fully undertaken CAD data exchange matters in FORAN and developed numerous algorithms and solutions:
FORAN regularly deals with huge models with plenty of parts ranging from big ones like ship hulls to tiny screws. As a result, such models may load too slowly, and moving them in a 3D scene makes up just another ugly problem for engineers. They might open a model just to take a quick look at it and end up waiting for several minutes.
To eliminate the problem CAD Exchanger added support of multiple LODs (Levels of Detail). Implementing this feature for formats other than JT was not as straightforward and required care to represent LODs in ways that are native to these formats. But it was ultimately worth it, as it became possible to import and export models with several polygonal representations in FORAN: from coarse to fine one. Now the parts unnecessary at this or that design stage can be loaded in lower quality and thus faster.
One of the problems SENER experienced was that their clients started noticing the slowness of the geometric algorithms used for weld search, plates and profiles modeling, and others. CAD Exchanger team examined and profiled the FORAN’s code in order to find out the exact reasons for the algorithms going sluggish. The suggested solution included data race causes identification and the implementation of computational parallelism. The suggested solutions included the implementation of parallelism in computations and more nuanced usage of geometric operations. As often happens, introducing parallelism in complex computation code was a non-trivial process with numerous problems lurking (data races, thread contention). Ultimately, CAD Exchanger's efforts allowed to speed up aforementioned algorithms to a varying degree, with some accelerating 10X for medium-sized models and up to 60X for large ones.
Most of the models imported into the FORAN system are represented by the B-Rep geometry, while FORAN itself operates with a set of predefined higher-level parametric geometry objects, from simple primitives (e.g., box) to more advanced (e.g., pipes, valves). The latter is more preferable as parametrics are inherently more informative and have a lower memory footprint. To improve the performance of working with the external models, CAD Exchanger played a key role in the development and integration of algorithms to automatically recognize FORAN parametric objects from the original B-Rep models.
When importing models into FORAN, the user has an option to create 2D views of the model for drawing generation. Initially, optimal results were provided only for FORAN parametric objects. In the case of B-Rep and polygonal geometry, the projection consisted of excessive information and required additional manual processing. To simplify the user's workflow, CAD Exchanger developed a hidden line removal algorithm that identified the visible faces, edges, and triangles for a specified view and thus enabled the creation of the B-Rep and mesh model projection into a 2D plane.
The next step was to boost the performance of the method. CAD Exchanger implemented computational parallelism for several stages of the algorithm. Speeding up projection generation up to 5X for B-Rep models and up to 8X for mesh models provided a better user experience for FORAN customers.
More to come
FORAN is constantly moving towards digitalization and upgrading its data model to ensure the best user experience in creating better ships at a lower cost. Therefore however many improvements have already been implemented into the system, CAD Exchanger has yet to make a lot. Among the current projects, there are two particularly noteworthy ones:
As mentioned before, FORAN stores just the minimum set of CAD data to keep the processes fast. However, when it’s necessary to export the model, the recreation of its parameters from the FORAN’s data model takes a lot of time. Accordingly, it was agreed to accelerate the process with multithreading, drawing on CAD Exchanger’s experience of parallel computation. This technology will improve the overall efficiency of the CPU and the resulting user experience.
OCX (Open Class 3D Exchange) is a new data exchange format between shipbuilding CAD software and classification societies tools. These latter approve the ship’s design or send it back to the designer with annotations on necessary improvements. As the format finds acceptance both among classification societies and shipbuilders, the ability to robustly export data to OCX will become a vital feature for FORAN.
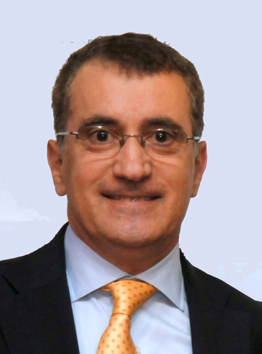
Jesús Ángel Muñoz Herrero
Ship models exported to OCX will enable FORAN users to streamline the process of classification, integrating it with CAD, CAM, CAE, and PLM processes and avoiding the need for additional data extraction and exchange.
Scaling user experience and keeping up with the multi-CAD world
SENER Marine shipbuilding expertise together with CAD Exchanger competence in 3D data is a part of a force moving FORAN system towards the digital transformation of Industry 4.0. According to Jesús Ángel Muñoz Herrero, FORAN System Product Manager at SENER Marine, throughout a decade, this collaboration allowed them to provide customers with up-to-date shipbuilding-oriented features, seamlessly backed by constant data exchange improvements.
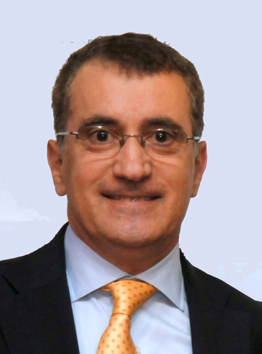
Jesús Ángel Muñoz Herrero
Starting with specific formats supports, CAD Exchanger managed to shoulder their full responsibility for 3D data exchange and skyrocket the performance of the FORAN system with the numerous algorithms development:
- JT, STEP, IGES, DXF, IFC, and other formats support
- Faster models loading via multi-LODs
- Performance boost via computational parallelism up to 60X
- Parametric body recognition
- Hidden line removal (HLR)
- B-Rep and mesh models simplification
- Export from FORAN data model to OCX
Covering the whole range of CAD-specific issues, CAD Exchanger let SENER Marine reduce FORAN’s go-to-market time, increase its value with the rapid development of new features, and just make their product run smoother and faster.
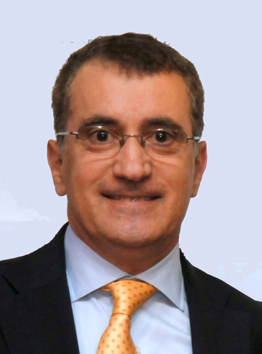